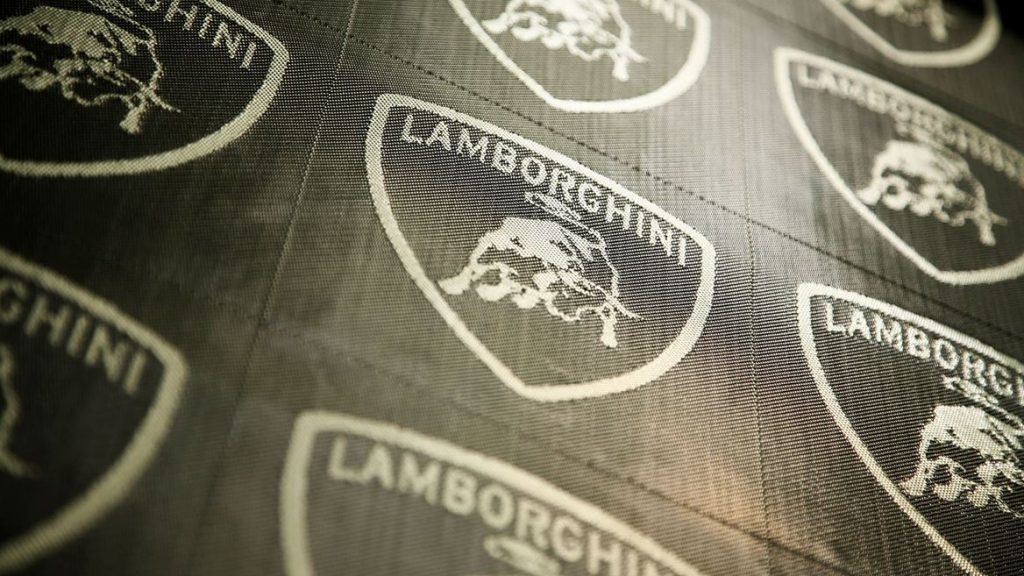
Sant’Agata Bolognese – Uno dei punti di forza della strategia di Automobili Lamborghini nella progettazione dei suoi prodotti è lo sviluppo e l’applicazione di materiali leggeri in fibra di carbonio. Le continue sperimentazioni e l’approccio innovativo hanno contribuito in oltre 35 anni a rendere la Casa del Toro un leader assoluto in questo settore. Di seguito le 12 tappe di questa storia straordinaria:
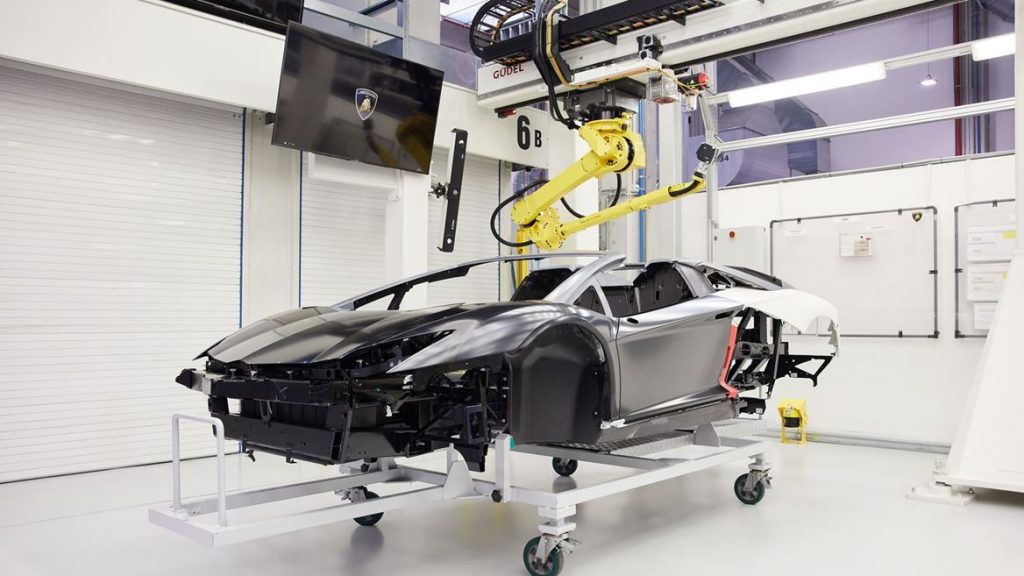
1983: Lamborghini avvia per la prima volta lo sviluppo e l’utilizzo della fibra di carbonio. Nel nuovo Reparto denominato ‘Esperienza Materiali Compositi’ (E.Co), avviato grazie all’arrivo da Seattle delle conoscenze sviluppate sui primi componenti in fibra di carbonio e kevlar del Boeing 767, nasce il primo prototipo di telaio in Carbonio della Countach chiamata per questo Evoluzione. È questo il primo progetto Lamborghini dove vengono utilizzati materiali compositi e primo progetto in assoluto di questo genere per una vettura stradale.

2007: instaurata una stretta collaborazione con l’Università di Washington (UW), una svolta importante nella storia dei compositi in Lamborghini. All’ateneo statunitense vengono delegati alcuni aspetti fondamentali di sviluppo per la tecnologia out-of-autoclave in RTM, tecnologia che poi sarà la base della monoscocca della futura Aventador.
Dal 2007 è stata inoltre costituita una divisione all’interno dell’area di Ricerca e Sviluppo, oggi chiamato “Centro Sviluppo Compositi”, che si occupa della ricerca di materiali innovativi e dello sviluppo di nuovi concetti e tecnologie applicati alla fibra di carbonio.
2008: siglato il primo accordo di collaborazione con la Boeing per studiare il comportamento a crash del materiale composito e della futura monoscocca della Aventador. Automobili Lamborghini, prima di tutti in ambito automotive, inizia ad implementare tecnologie, processi e metodi di simulazione e caratterizzazione dei materiali compositi propri dell’aeronautica e dell’industria aerospaziale.
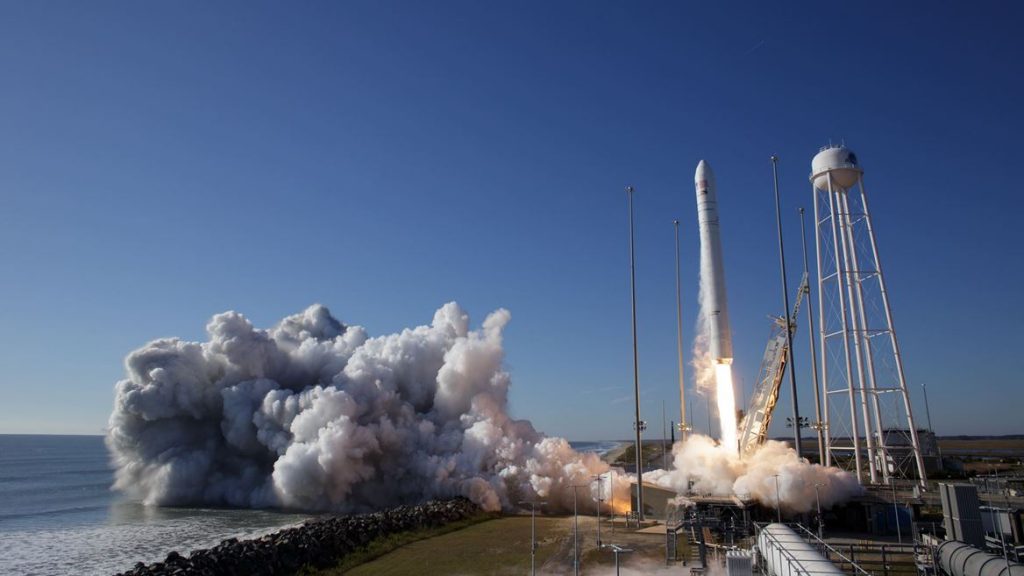
2010: grazie alla collaborazione con Boeing e Callaway, Lamborghini sviluppa la tecnologia Forged Composites®, brevetto specifico attorno al quale nell’arco di pochi giorni nasce l’idea della supercar Sesto Elemento. Nello stesso anno viene costruito all’interno del sito produttivo Lamborghini un impianto dedicato alla produzione di componenti in materiali compositi (successivamente destinato alla produzione della monoscocca della Lamborghini Aventador), che alterna fasi di produzione automatizzata a fasi di accurato lavoro artigianale.
2011: debutta la nuova Aventador LP 700-4, dotata di un’innovativa monoscocca in carbonio ideata e prodotta interamente dalla Casa di Sant’Agata Bolognese. La scocca dell’Aventador, realizzata interamente in fibra di carbonio, nonché progettata con una struttura unica, garantisce un telaio con un peso di soli 229,5 kg. Proprio per l’unicità e complessità del processo di produzione della monoscocca in materiale composito, che nessun fornitore è in grado di gestire, Lamborghini decide di produrre internamente la monoscocca.
La maggior parte degli elementi della monoscocca sono prodotti con la tecnologia brevettata da Lamborghini “RTM-Lambo”. Questo processo rende superflua la laminazione manuale e l’utilizzo di autoclavi e allo stesso tempo permette di usare stampi in fibra di carbonio, riducendo così i tempi di lavorazione e facendo così della RTM-Lambo una tecnologia di produzione decisamente all’avanguardia.

Nel 2011 inizia inoltre lo sviluppo della strategia del repair attraverso una nuova collaborazione con Boeing.
2014: Automobili Lamborghini ottiene, come prima azienda automotive al mondo, la certificazione da TÜV per il servizio di riparazione delle vetture in fibra di carbonio. Il servizio di repair, il cui sviluppo è iniziato nel 2011, ottiene la certificazione per i requisiti di responsabilità, tracciabilità, affidabilità, tempistica e puntualità del servizio offerto, a seguito di una fase di audit condotta dagli esperti TÜV Italia. Il servizio viene offerto attraverso l’impiego di figure professionali specializzate, denominate “Flying Doctors”. Si tratta di figure professionali che hanno seguito inizialmente un percorso di formazione presso il Dipartimento di Repair della Boeing Co., approfondito in un secondo momento presso la Abaris Training Resources Inc. in Nevada dove hanno ottenuto la qualifica di Advanced Composite Structures Damage repair, riconosciuta dalla americana Federal Aviation Administration. L’obiettivo alla base del repair definito da Lamborghini è quello di garantire che le caratteristiche tecniche prestazionali siano identiche al 100% a quella della parte originale.
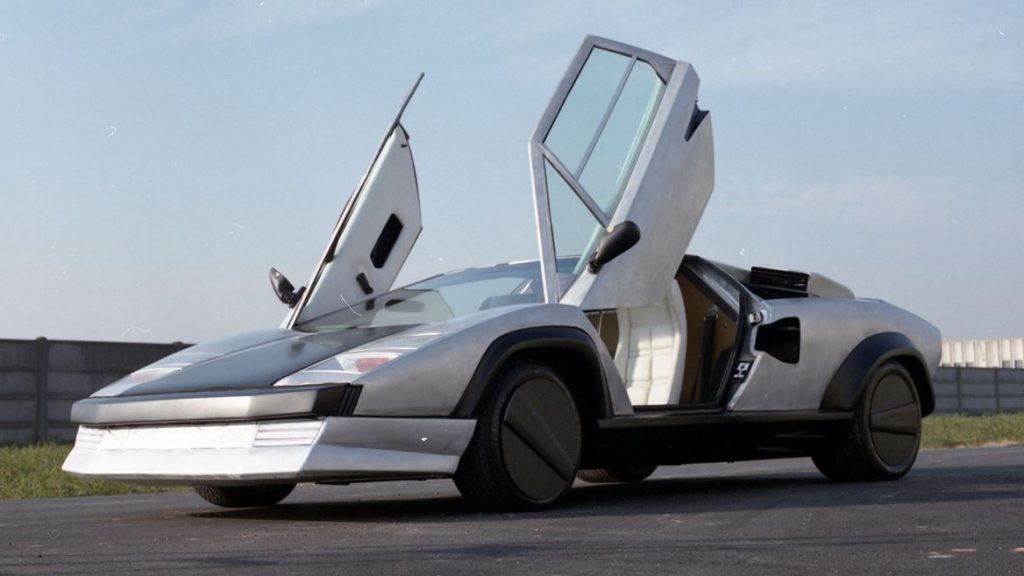
2015: nasce il Carbonskin®. Automobili Lamborghini estende il proprio raggio d’azione nel campo dei materiali flessibili e, dopo anni di ricerca e sviluppo, concepisce un nuovo materiale in fibra di carbonio con matrice flessibile, adatto all’applicazione negli interni della vettura. Nasce quindi il Carbonskin®, altro brevetto esclusivo di Lamborghini, un materiale composito flessibile qualificato per l’Automotive unico nel suo genere. Il Carbonskin® è stato sviluppato interamente dal team di Ricerca e Sviluppo di Automobili Lamborghini e rispetta tutte le richieste omologative e di validazione previste nel mondo automotive. Questo materiale innovativo offre oltre al risparmio di peso (-28% per Alcantara e -65% per la pelle), caratteristiche estetiche uniche come la naturalezza della fibra di carbonio, l’effetto tridimensionale e la sua morbidezza immediatamente percepibile al tatto se paragonata a qualsiasi altro materiale.
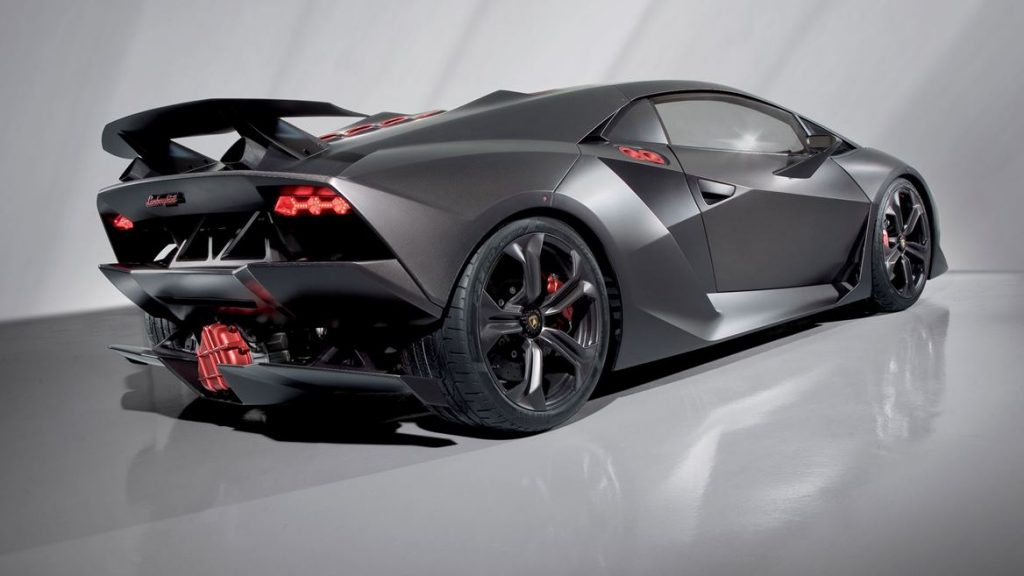
2016: inaugurato il nuovo laboratorio dedicato alla ricerca sulla fibra di carbonio, l’Advanced Composite Structures Laboratory (ACSL) a Seattle (Washington, Stati Uniti). Operante come entità esterna alla sede centrale dell’azienda a Sant’Agata Bolognese, l’ACSL si occupa di analizzare le nuove potenzialità racchiuse nella fibra di carbonio.
2017: progetto di ricerca con lo Houston Methodist Research Institute per lo studio dei materiali compositi in ambito medico. Automobili Lamborghini mette a disposizione del Houston Methodist Research Institute il proprio know-how nello studio dei materiali compositi in fibra di carbonio, avviando una collaborazione per lo studio dei medesimi materiali in ambito medico. Il progetto di ricerca verte sullo studio della biocompatibilità in-vitro dei materiali compositi, che potranno essere poi eventualmente impiegati per lo sviluppo di impianti protesici, ma anche per dispositivi sottocutanei. Lo scopo è quello di individuare nuovi materiali che possano essere più leggeri, radio-trasparenti, meglio tollerati dal corpo umano e più resistenti nel tempo rispetto a quelli attualmente impiegati in ambito medico.
2019: test nello spazio. Automobili Lamborghini è la prima casa automobilistica al mondo ad avviare ricerche su materiali in carbonio a bordo della Stazione Spaziale Internazionale ISS. L’attività congiunta di ricerca sui materiali compositi avanzati in fibra di carbonio, avviata due anni prima da Automobili Lamborghini e Houston Methodist Research Institute, giunge ad un importante punto di svolta. Il 2 novembre 2019 avviene il lancio del vettore Northrop Grumman Antares dalla Wallops Flight Facility in Virginia, con la missione di portare a bordo della Stazione Spaziale Internazionale (ISS) un set di campioni di materiale composito realizzati da Automobili Lamborghini. Il lancio si inserisce nel quadro di una campagna di test sponsorizzata dall’ISS U.S. National Laboratory e sovraintesa dal Houston Methodist Research Institute. In particolare questi test sono mirati ad analizzare la risposta di cinque differenti materiali compositi prodotti da Lamborghini alle sollecitazioni estreme indotte dall’ambiente spaziale, in vista di future applicazioni su modelli della Casa di Sant’Agata Bolognese e in ambito medico.
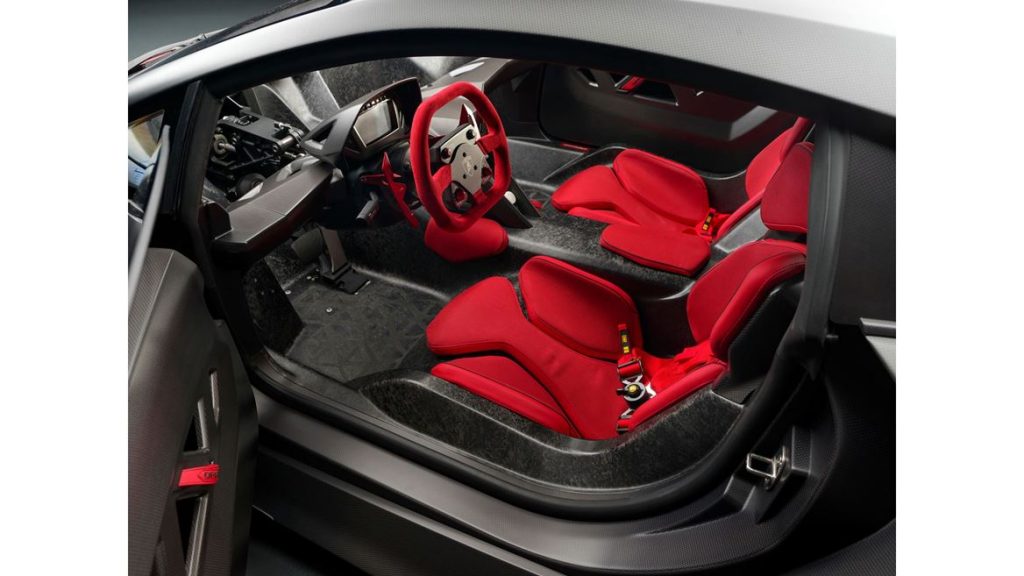
2021: debutta la Lamborghini Essenza SCV12, prima vettura sul mercato con roll cage in carbonio omologato secondo gli standard di sicurezza FIA Hypercar. Un traguardo straordinario frutto dell’esperienza trentennale di Automobili Lamborghini nello studio e applicazione dei materiali compositi in ambito automotive.
Per raggiungere questo risultato la monoscocca in carbonio, prodotta a Sant’Agata Bolognese nelle autoclavi del reparto CFK di Automobili Lamborghini, è stata rinforzata in più punti, dovendo sopportare forze di oltre 12 tonnellate senza presentare deformazioni di rilievo durante i test estremamente rigorosi sia di tipo statico che dinamico per l’omologazione FIA. I test statici sono stati più di 20 e hanno coinvolto oltre al telaio, anche la pedaliera, le cinture ed il serbatoio carburante. I crash test dinamici invece hanno previsto impatti a velocità fino a 14 metri/secondo ed è importante sapere che in questo tipo di prove il telaio non deve subire intrusioni di elementi esterni che possano entrare in contatto con il pilota e il serbatoio non deve presentare perdite di carburante.
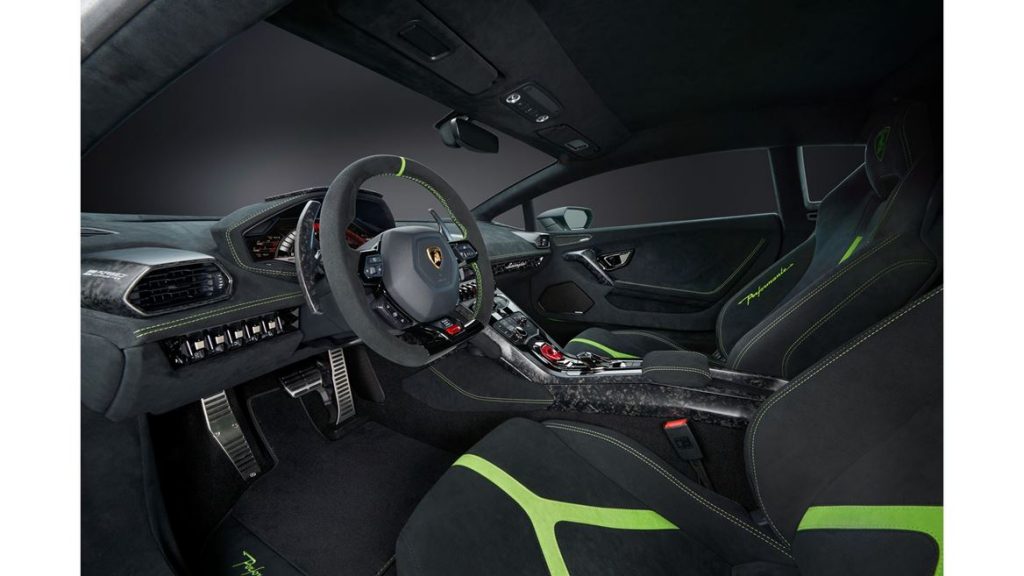
Oggi: sostenibilità e riciclo degli scarti. Un ulteriore aspetto su cui Automobili Lamborghini sta lavorando da anni è quello della sostenibilità ambientale dei processi di produzione dei materiali compositi. Oggi, gli studi e i progetti portati avanti dai tecnici Lamborghini hanno portato alla scelta di specifiche tecnologie di produzione che vanno a ridurre i consumi energetici e di risorse preziose come l’acqua e vanno a ridurre drasticamente gli scarti del materiale composito.
Questi vengono riutilizzati in altre applicazioni sia su vettura che per usi interni come pannellature e carrelli. Quello che non è riutilizzabile viene raccolto e riciclato per recuperare la fibra e realizzare dei nuovi prodotti di “carbonio riciclato”, che possono essere utilizzati per la realizzazione di altri componenti vettura richiedenti minori caratteristiche strutturali ed estetiche, come ad esempio i fondi vettura. Inoltre, gli scarti di processo vengono utilizzati per realizzare sottoprodotti come gadget per i clienti e gli ospiti durante gli eventi organizzati da Lamborghini. Tutto questo nell’ottica di creare una vera e propria sostenibilità circolare della fibra di carbonio.
Post simili
CUPRA Tavascan Experience: fa tappa anche a Bergamo il viaggio lungo lo stivale targato CUPRA
Oltre 30.000 visitatori alla State Opera per tutti e BMW Classics.
Imparare per il futuro – con l’intelligenza artificiale e la realtà virtuale